Water damage is one of the most destructive issues homeowners and property managers face. It’s also often expensive and difficult to repair.
There are several ways to prevent water damage. By taking preventative measures and regularly performing maintenance, you can reduce the likelihood of water-related issues. These include water supply line breaks, broken dishwasher hoses, flooding from natural disasters, and clogged toilets.
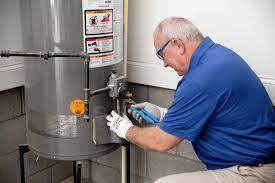
Water heaters are a vital part of a home, but they also present the possibility of serious damage. A water heater that leaks can cause a major flood, damaging floors and carpeting as well as drywall. Sometimes, the water can seep into studs and support beams, requiring replacement. Water that pools under a water heater can warp floorboards and crack baseboards, causing costly repairs.
Loose fittings, overheating, or corrosion can cause leaks from a hot water tank. A leaking water heater is considered a major safety hazard and should be replaced immediately. Water damage from a leaking hot water tank can be prevented with regular maintenance, proper temperature and pressure settings, insulation, replacing old tanks, and regular checks for rust streaks.
If you notice a pool of water under your water heater or hear loud banging, clanging, and popping sounds, it’s important to turn off the water supply line at the valve on your water heater. After locating the supply line, twist the valve clockwise to turn off the water flow.
It’s also important to understand your homeowner’s insurance policy and the type of water damage it covers. Typically, if a water damage claim is accidental and not due to your negligence, the water damage will be covered. However, it would help if you also considered purchasing additional personal property coverage if the water damage is severe and you need to replace your water heater.
Washing machines are used more often than most other large household appliances and are thus subject to stress and wear. They are also under the full pressure of your home’s water supply 24/7 and can be prone to leaks and bursts. A leaking or flooding washing machine is more than just annoying; it can also be costly.
The most common cause of a washer flood is a clogged drain pipe. Utility sink drains are often used for everything from paint trays and brushes to pet bowls and muddy shoes so that they can get a lot of “stuff” washed down them. If that stuff gets caught up in the pipes and restricts water flow, it can lead to overflows and flooding.
Another common reason for a washing machine to flood is if it’s overloaded. This can strain the hoses excessively and cause them to break or develop cracks. The best way to prevent this is to use smaller loads and follow the manufacturer’s guidelines for load capacity.
It’s also a good idea to regularly inspect all your appliances and water hoses for any signs of damage, wear, or leaks. If your hoses are over five years old, consider replacing them with stainless steel braided ones, which are more durable and less likely to leak. It’s also a good idea to turn off your washing machine valves when not in use and to keep the laundry room and drain pipes clean.
For homes with refrigerators that produce ice water, the hoses connected to the appliance are often the source of slow leaks and flooding. These tiny hoses are subject to frequent use and can develop problems from repeated freezing and thawing, pinched sections, or simply aging over time. Since the hoses are usually hidden, these issues can go unnoticed until puddles form under the fridge or ice production declines.
These hoses can quickly infiltrate the kitchen floor and walls when they break. They can also lead to wood rot, mold growth, and staining. It is important to call a professional as soon as you discover water damage so the remediation process can begin promptly to minimize structural damage and prevent lingering odors.
The first step is to turn off the water supply valve, normally found underneath a sink or behind the refrigerator. Then, you can disconnect the hose from the refrigerator and inspect it for a broken or cracked section. If you notice a water line leaking, it is best to call in a technician or, if you are confident enough, order a replacement hose and swap it out yourself. If you have a home insurance policy, then most insurers will cover the cost of replacing the piping and flooring that the leak has damaged. However, homeowners insurance typically only covers water damage caused by sudden, accidental incidents.
Fire sprinkler systems are designed to disperse water when high heat is detected. However, these systems can fail for a variety of reasons. If your home or office has a fire sprinkler system, keep it in good working condition to prevent water damage.
One of the main causes of fire sprinkler malfunction is human error. Employees often accidentally hang items from a sprinkler head or run into it while using a forklift. These mistakes can trigger the sprinkler head, resulting in extensive water damage.
Another common cause of fire sprinkler water damage is weather conditions. Because fire sprinkler piping is constantly filled with water, it can be exposed to freezing temperatures during colder times of the year. This can result in ice forming inside the pipes, creating leaks or even rupturing the pipe.
Finally, corrosion can also lead to fire sprinkler system failures. Sprinkler piping is often made of steel or brass, susceptible to corrosion. Corrosion can cause the piping to break down or burst, leading to floods or excessive water pressure.
Water tanks are a valuable asset for storing emergency water in a disaster. They can also be used for firefighting in fire-prone areas. However, these tanks must be properly maintained to avoid water damage. This can be accomplished by ensuring the tanks are located safely and their overflow pipes are correctly sized based on the maximum incoming flow rate. It’s also important to include (sludge) drains on water storage tanks so they can be drained easily.
Corrosion on steel tanks is a common problem and can cause leaks and water damage. This happens because the tank’s cathode, or water-covered surface, attracts electrons from the anode or non-water-covered surface. When this occurs, the tank can weaken or even break. Water tanks should be placed in a dry location away from sunlight to prevent corrosion.
Plastic tanks are less susceptible to damage than steel tanks. They are available in various shapes and sizes to suit different needs. They are often designed to be durable and resistant to extreme climate conditions. They are also shielded from sunlight by UV inhibitors. Additionally, they are food-grade safe and are BPA-free.
When a plastic rooftop water tank leaks, several steps should be taken immediately; first, turn the water supply off. This will prevent additional water from entering the tank and exacerbating the leak. Next, drain the water tank by attaching a hose to its drain valve.
Water supply lines are pressurized pipes that deliver water to sinks, faucets, washing machines, dishwashers, toilets, showers, and other appliances. These water lines can break for many reasons, including age, extreme cold, soil shifts, damage from excavation machinery, and more. When they fail, the leaking water destroys drywall, flooring, cabinets, and wood. It can also cause mold.
Water line breaks can happen anywhere on your property and can be difficult to locate. The first sign is usually a sudden drop in water pressure from all sources. Another symptom is puddles in your yard. If you notice these signs, contact a plumber right away.
If a water main break affects your neighborhood, you might receive Boil Water Advisory warnings from the local water department. All tap water must be boiled before use because dirt and other contaminants may be introduced. This can be expensive for businesses that rely on ice and soda machines, leading to a loss of business.
When a water line breaks, it can be very dangerous and must be repaired immediately. If you live in a city, the water company is responsible for fixing this problem, but they need to know exactly where the break is. This requires visual inspection, listening with correlating equipment, and sometimes excavating. To do this, they must coordinate with up to five utility companies.